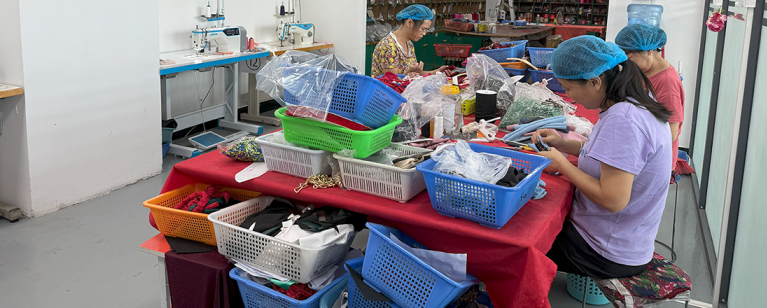
Common framework for responsible purchasing practices
Principle 1: Integration | Principle 2: Equal Partnership | Principle 3: Collaborative Production Planning | Principle 5: Sustainable Costing
Responsible Purchasing Practices in Manufacturing Initiative
The garment and footwear industries have long been at the forefront of efforts to address responsible purchasing challenges, largely due to external scrutiny and pressure. While unethical practices remain, this scrutiny has been instrumental in driving a greater understanding of responsible practices.
However, manufacturing industries outside of textiles have often received less attention in this area. Running from June 2023 to February 2025, ETI's initiative, funded by the German Development Cooperation (GIZ), sought to address this gap by exploring how the principles of the Common Framework for Responsible Purchasing Practices (CFRPP) could be applied to manufacturing sectors and improve human rights outcomes within supply chains.
Over the course of 21 months, ETI assessed manufacturing businesses in improving their purchasing practices and evaluated the effectiveness of the measures implemented. The project engaged diverse stakeholders groups through surveys, group consultations, and direct advocacy with companies, helping to deepen the understanding of how buyers and suppliers engage in purchasing practices and their human rights impacts.
Introduction
Smallworld Accessories, a fashion accessory company primarily operating through concession models for large high street retailers, has been a member of the Ethical Trading Initiative (ETI) since late 2017, achieving full membership by 2020. With eight tier one suppliers in China and one in India, the company has always believed in fostering close relationships with its suppliers. However, an audit in 2020 uncovered a significant non-compliance issue concerning workers' wages. This discovery prompted the company to reassess their supplier relationships, recognising that compliance audits alone could not address the deeper, systemic issues affecting workers. Instead, more consistent and meaningful engagement with suppliers was necessary.
The company participated in ETI’s Responsible purchasing practices in manufacturing initiative, supported by the Initiative for Global Solidarity (IGS), which aimed to operationalise the Common Framework on Responsible Purchasing Practices (CFRPP) for the manufacturing sector. Between June 2023 and February 2025, participating companies were encouraged to review their purchasing practices and assess their potential contributions to human rights risks within supply chains. The initiative also facilitated supplier surveys and pilot projects designed to address these issues in selected supply chains.
Identifying challenges
When Smallworld joined the Responsible purchasing practices in manufacturing industries initiative, the company felt they were starting from a strong position. They had already made significant progress in improving practices since 2017, but they were open to new perspectives. As part of the initiative, Smallworld completed various exercises to assess their policies and practices. The company also participated in a supplier survey facilitated by ETI, to better understand how their purchasing practices were impacting suppliers. All their tier one suppliers responded openly, and Smallworld recognised the importance of understanding the practices of their buying agent. They distributed a separate survey targeting the agent’s operations, and the results revealed several challenges faced by suppliers that could have detrimental effects on workers.
Suppliers identified the following issues in their relationship with Smallworld:
- Failure to adhere to the critical path
- Excessive sampling
- Changes to product designs after orders had been placed
- Inconsistent and imbalanced orders throughout the year
- The potential to streamline product designs for cost savings
These issues were also linked to labour rights risks, including:
- Excessive working hours
- Reliance on temporary workers and subcontracting
- Stress among workers
Julia Robertson, Head of Buying and Design at Smallworld, shared:
“We thought we were doing quite well—we thought we were on our critical path, and we considered ourselves a responsible company. But it became apparent that there was more work to be done and improvements to be made. It was clear that the key issues that were consistently raised by our suppliers really did affect working conditions for the factory workers—whether that be long hours, stress, or working under pressure. And we’re just not happy with that. We are very pleased to be involved in this initiative because, in addition to the work we’ve done already, it is giving us more insight and a very clear direction on what actions need to be taken to make these improvements.”
Responding to the challenges
In response to the survey results, Smallworld embraced the opportunity to participate in a pilot program with two suppliers to gain deeper insights into their purchasing practices. The pilot involved direct engagement with workers through interviews and focus groups to better understand working conditions and assess the impact of Smallworld’s purchasing decisions. As the pilot evolved, valuable insights were gained, highlighting areas for further improvement, including formal contracts, grievance mechanisms, and clearer communication around pay structures. These findings have provided a clear direction for Smallworld to enhance its practices and foster positive change within its supply chain.
Smallworld took the following steps in response to the findings:
- Monitoring the product hit rate (aiming for an increase from 30% to 60%)
- Reevaluating lead times for products based on complexity
- Ensuring all permanent factory workers had signed contracts and understood their wages
- Discussing the establishment of worker unions and committees with factories
- Addressing excessive overtime while ensuring no adverse impact on worker wages
Impact on suppliers
Principle 2: Equal partnership
In a follow-up survey, all Smallworld’s suppliers reported an improvement in their relationship with the company. Over 60% of suppliers noted that communication had "much improved," and more than half felt that purchasing and business decisions had significantly improved. Suppliers appreciated Smallworld’s commitment to sharing more market data and explaining the critical path more clearly.
One factory business manager from Dongguan Fenghe shared:
“This project model is excellent. We have never experienced this approach before. We can communicate honestly and openly with the client, who treats us like their own factory and hopes to achieve business growth together. Our factory has gained substantial benefits and assistance in this process.”
The improved communication allowed suppliers to give honest feedback on how better production planning, more evenly spaced orders, and clearer communication could benefit their workforce, reduce reliance on temporary workers, and improve their bottom line. These suggestions were promptly taken on board by Smallworld.
Principle 3: Collaborative production planning
At Small World, changes in purchasing practices, such as improving the hit rate and adjusting lead times, have been positively received by suppliers. The collaborative approach has fostered honest feedback and helped suppliers feel more engaged and invested in the process.
As part of their commitment to transparency and collaboration, Smallworld ensures that all orders must be raised from an approved sample. Suppliers are fully informed that they are entitled to reject an order if they believe the approval process hasn’t been completed. To further strengthen this partnership, Smallworld will provide feedback on hit rate analysis after every sign-off and is working on an individual critical path for each factory. This includes projected forecasts and order-raising dates. Suppliers will have visibility into key milestones, such as when designs will be sent, when samples need to be ready and in the UK, when range building and negotiations will occur, and when the final order will be raised. By tracking these timelines together, Small World and their suppliers can monitor whether order projections are being met. After one year, Small World expects this process to stabilize, enabling suppliers to better manage their workforce.
Small World is focused on smoothing out the peaks and troughs in their production schedule to reduce reliance on short-term or migrant labor. This shift will ultimately benefit contracted and permanent employees by providing greater workforce stability.
Impact on workers
Although the changes did not yet have a direct impact on workers in late 2024, visits to the factories in early 2025 showed that workers supported the changes. Many factory workers expressed their preference for the new approach to communication, which was more informal and open. One worker from Qingdao JYXH stated:
“Previously, we mostly had client audits, in which the auditors would apply a Q&A approach, which made us very nervous. However, this project involves communication through casual conversations with workers, and we feel more at ease.”
Follow-up surveys of suppliers indicated that the changes, particularly improved production planning and clearer communication, were expected to reduce overtime hours in certain months and increase enthusiasm among workers.
Additional benefits
Although the direct effects of the purchasing practices changes have yet to be fully realised by workers, the pilot program facilitated several worker rights improvements. In one factory, all employees received new contracts with clear terms, something that had not been in place before. In another, a new grievance mechanism was introduced, and signs were posted throughout the factory to promote awareness of the system.
Impact on Smallworld
The changes implemented through the pilot project have already benefited Smallworld in several ways. Improved supplier relationships and clearer critical path planning have helped the company gain greater visibility into their supply chain. Smallworld was granted access to tier two suppliers, which had not been the case before, allowing the company to better understand the challenges and opportunities within their extended supply chain. This newfound transparency will help Smallworld improve the resilience of its supply chain and better prepare for future supply chain due diligence regulations.
The company expects to benefit from improved production efficiency, especially as the hit rate improves, reducing the need for excessive sampling and saving both time and money. Smallworld’s supplier critical path with accurate planning is expected to save costs and directly benefit permanent workers by creating a more streamlined, predictable production process.
During a recent trip in March 2025, Smallworld had the opportunity to review feedback from suppliers through questionnaires, which led to a very positive meeting. Discussing challenges and expectations in an open forum facilitated constructive dialogue and fostered a sense of trust and collaboration. For the first time, factories have been open to discussing all aspects of the production process, including open costings.
“There is an openness that we haven’t had before, and a commitment from all to work together in partnership to improve ways of working. The open costing means that we have visibility of their low-margin lines, and vice versa. This transparency helps when it comes to negotiating and finding alternatives in a fair and open way,” said Julia Robertson, Head of Buying and Design at Smallworld.
To further enhance collaboration, Smallworld has offered to pay for excessive sampling, recognising that, while this is an important consideration, excessive sampling impacts worker morale and stress levels—especially when designs that have been sampled are not ultimately ordered. Recognising the emotional and financial toll this can take, Smallworld is working to balance cost with supplier well-being. Additionally, to build morale, Smallworld will be sharing information on factory bestsellers, providing a sense of pride and achievement for workers and creating a more positive working environment.
Takeaways
Smallworld’s participation in the Responsible purchasing practices in manufacturing initiative has provided valuable insights into how its purchasing decisions can better align with positive human rights outcomes. Through meaningful engagement with suppliers and workers, Smallworld gained a deeper understanding of the challenges within its supply chain and identified key areas for improvement. While ongoing efforts will continue to address challenges such as overtime, wage structures, and worker representation, the company is committed to making lasting improvements that will enhance conditions for workers and strengthen its supply chain.
This case study demonstrates the value of a holistic approach to addressing purchasing practices and human rights due diligence. By fostering open communication with suppliers and workers, Smallworld has strengthened its supply chain and paved the way for future improvements that will benefit both workers and the business.
Responsible purchasing practices in European legislation
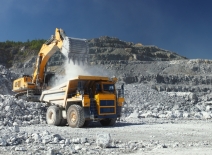