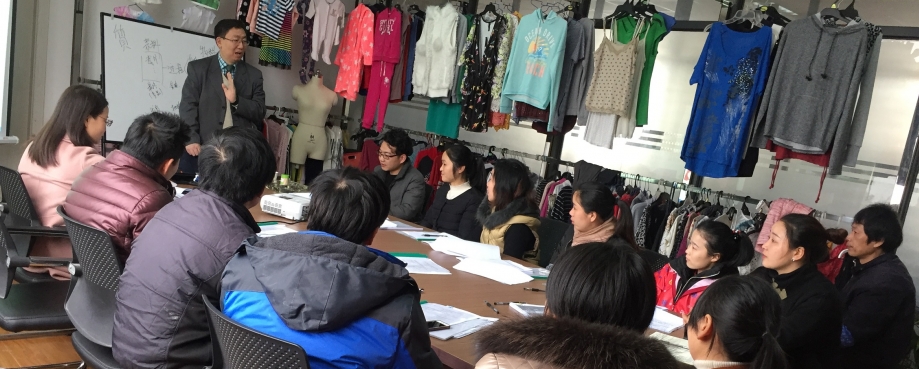
Steve Wickham, Head of Corporate Social Responsibility at Matrix APA (UK) Ltd., blogs for us on how a partner factory in China, the Xiangshan Dasheng Knitting Co Ltd. is putting ETI/ILO Score training on improving management and workforce relations into practice.
“Can I have some water please?”
A simple enough question with a simple answer in most circumstances, but not for factory workers attending an ETI/ILO SCORE Training module on Quality Management.
This simple question was used as a practical example of the importance of understanding customer needs and asking the right questions: “Would you like hot or cold water?” “What temperature?” “Do you prefer a cup or a glass?”
These are things that Five Star hotels do well around the world as they maintain a healthy focus on ‘what their guests need’ and it’s a great example for factories to follow to help them manage customer expectations in a proactive way.
This and other valuable lessons on quality management formed part of the SCORE training session I was fortunate to observe at Xiangshan Dasheng Knitting Co Ltd. during my visit to China in January.
Shared benefits for workers, suppliers and customers
As a company, Matrix is a multi-category product design and procurement specialist with a focus on ethically sourced products and building long term co-operative partnerships with our suppliers in Asia.
Central to our business model is a belief in the shared benefits for workers, suppliers and customers that can be gained from driving positive change in working conditions.
That’s why we were so interested in encouraging participation in the Score Training project.
It helps small and medium sized enterprises (SMEs) to improve working conditions and productivity through implementation of practical changes to the workspace and knowledge building of internationally renowned methodologies.
Easily implemented improvements
ILO trainer, Jia Hongwei, was experienced in relating the topics to practical examples that meant something real to the workers and, more importantly, could be easily implemented immediately after the training.
The areas covered during the interactive classroom session included:
- The importance of establishing Standard Operating Procedures (SOPs) and how to write them?
- How to encourage healthy competition in the workplace to improve productivity with team names and league tables of performance?
- how to reward workers good suggestions based on a percentage of the value of the idea to the business?
It was also interesting to see how the training material engaged employees from all different levels including managers, line leaders and production workers, with different examples being used to ensure the topics are fully understood by everybody present (including myself as an observing brand partner!).
Corrective actions and measures
The crucial difference between corrective actions and corrective measures was a case in point when the trainer engaged everybody with a story of how, when confronted with the problem of an infestation of flies in the workshop, one factory manager’s suggested action was just to “swat the flies."
It was a SCORE-minded production worker, however, who proposed the more effective corrective measure of “closing the windows!"
Such examples and relatable stories not only help to bring SCORE training material to life but help ensure that the benefits of joining the SCORE programme can be felt long after the training has ended.
To find out more about ILO and ETI SCORE Training contact Eshan Chan.
ETI-ILO SCORE training runs until February 2019 with funding from Germany’s Federal Ministry for Economic Cooperation and Development (BMZ) via its develoPPP.de programme. DevelopPPP helps German and other European companies conduct business activities in a responsible manner in line with the expectations of the Sustainable Development Goals. In the context of the SCORE initiative, ILO and ETI are cooperating with SEQUA, one of DevelopPPP’s designated partners charged with implementing the programme.