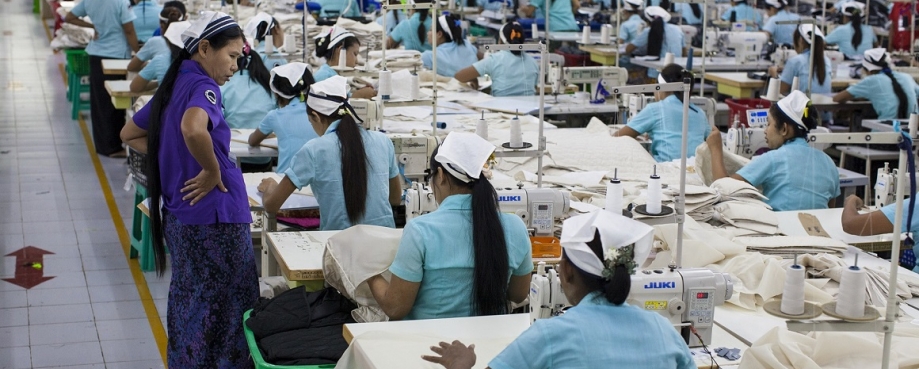
ETI member, Gap Inc. has published the names of the first tier factories from which it sources its garments, and is looking to update its list every six months. By doing so, Gap Inc. (Gap in the UK) joins a relatively small group of brands which have taken this step in a bid to improve their transparency commitments. ETI's Jane Moyo asked the company’s Vice President of Global Sustainability, David Hayer why Gap decided to go down this route.
In the course of his work, David Hayer visits dozens of factories globally; and after leading Gap’s sourcing offices in South Asia for two years knows the factories well.
David’s seen first-hand how some of Gap’s corporate social responsibility programmes, such as the P.A.C.E. initiative – a personal advancement and career enhancement programme – positively impact women workers in the company’s supply chains.
It’s led him and Gap to think further about how to improve standards, not only within Gap’s suppliers but across the apparel and textiles sector as a whole.
The greater the availability of information, the greater the opportunity to raise standards
“It’s increasingly obvious that the greater the availability of information, the greater the opportunity to collectively raise standards,” David says. “Additionally, ‘competitive advantage’ arguments around remaining silent no longer hold water. Gap is an innovative brand, and given the rate of change in apparel and how rapidly designs change, those arguments are just not so important as they were five years ago.”
Gap’s sourcing policies have changed a lot over the last five to six years. It used to source from 2,000 factories. That’s come down to approximately 900. David argues that this emphasis on what are “strategic relationships” has increased trust and the level of partnership.
Building trust is important to Gap. David confirms that many of their suppliers report that they feel their standing in the supply chain has been elevated by this initiative. Most importantly to Gap, so has that of their workforce. He says, “it increases the credibility of all, it is a selling point for suppliers.”
Suppliers and workers benefit from transparency
Gap’s finding that suppliers benefit from transparency is important, and will ring bells with other ETI members, many of whom are consolidating their sourcing base too; and are also progressively more willing to share information and to cooperate to ensure labour standards improve within their supply chains.
As David says, competitors can easily figure out what factories Gap is in. “They’re sophisticated, large businesses and often source in the same markets, if not factories.”
David is keen to point out that Gap’s customer base expects an ethical approach too. “We see a growing trend in consumers expecting transparency. Over time we think the publication of lists such as these will have a positive impact on customers.”
For the present, the challenge is not to rest on laurels. “It’s important to acknowledge that this is just one step on a longer journey,” says David.
Publication is part of a package of measures
David confirmed that publication of the list as well as the introduction of other sustainability measures – such as providing their suppliers with increased access to data and analysis of their Assessment and Remediation programme – was something that Gap felt was critical. That belief, as well as engagement, went right up to Board level.
It’s undoubtedly an exciting time to be working in corporate sustainability as David talks enthusiastically about the changes that Gap is driving forward. “While we are aware that other companies often look at moves Gap makes, we are also aware that we are just one of a growing group of brands which wants to further tip the balance towards transparency.
“We know there is much more work to be done and we remain committed to continuing to improve labour standards for the women who make our clothes,” David says.
“We believe it will benefit other companies to take such a step too. We are firmly convinced that the greater the visibility, the greater the chance of improved working conditions and that a collective approach is important to driving real change across the sector as a whole.”