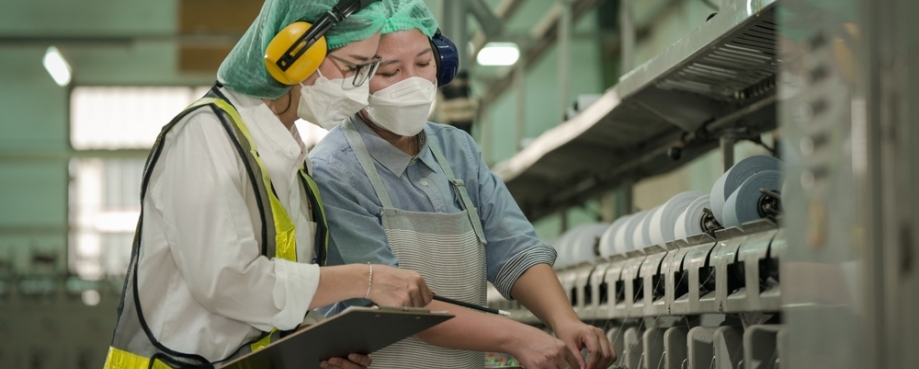
Manufacturing industries are constantly evolving, with companies facing increasing pressure to uphold ethical standards, particularly in relation to human rights and responsible purchasing practices (RPP). The fashion and footwear industries have long been at the forefront of efforts to address these challenges, largely due to external scrutiny and pressure. While unethical practices remain, this scrutiny has been key in driving a greater understanding of responsible practices.
But what happens when we apply the same responsible purchasing principles to manufacturing sectors? That’s exactly the question a project supported by GIZ and led by ETI has been seeking to answer. Through this initiative, ETI has examined how the Common Framework for Responsible Purchasing Practices (CFRPP)[1] ‘originally’ designed for the garment and footwear sectors can be adapted to address the specific needs and challenges of various manufacturing industries.
Why this matters: Expanding RPPs beyond the garment industry
Manufacturing industries have not received the same level of attention as sectors like garments and food when it comes to responsible purchasing practices. Running from June 2023 to February 2025, ETI’s initiative aimed to address this gap by exploring whether the principles of the Common Framework for Responsible Purchasing Practices could be applied to other sectors and to improve human rights outcomes in supply chains.
While fashion and food have seen a growing focus on responsible purchasing, industries such as electric vehicles, construction, cosmetics and stone have largely been overlooked. One of the few pieces of research on this topic is a 2017 report by the International Labour Organization (ILO) on the electronics sector, which found that high levels of outsourcing and multi-tiered supply chains lead to fluctuating demand, temporary contracts, and poor working conditions for workers.
ETI’s initiative sought to provide a comprehensive understanding of the challenges and opportunities of implementing responsible purchasing practices across a range of manufacturing industries. Through stakeholder surveys, group consultations, and direct engagement with companies and suppliers, the initiative aimed to understand how purchasing practices impact human rights, particularly workers' rights. By building on the lessons learned from this research, the Common Framework for Responsible Purchasing Practices in Manufacturing Industries (CFRPP MI) now offers guidelines that businesses can use to adopt responsible purchasing practices and improve working conditions in their manufacturing supply chains.
Overcoming initial scepticism
Initially, many companies were sceptical about the CFRPP, assuming certain practices didn’t apply to their business or that their influence was limited by power dynamics. While some of these assumptions proved accurate, many companies discovered that by focusing on the risks created by their own purchasing practices, rather than solely assessing risks within suppliers’ operations, they were able to shift the conversation. This allowed for a fundamentally different and open dialogue with suppliers, revealing that certain practices were indeed relevant to their industry.
Evolving the CFRPP: What’s different?
- Shift to universal language
A key change in adapting the CFRPP for manufacturing industries is moving away from sector-specific language to more general, universally applicable language. This shift better aligns the framework with EU regulations like the CSDDD, which governs human rights due diligence for in-scope businesses across sectors.
- A holistic approach to purchasing practices
It is vital businesses take a holistic approach to understanding and addressing the impacts of adjusting purchasing practices to avoid unintended consequences. For instance, better purchasing practices can improve production efficiency, as the critical path is optimised. This will reduce the burden on workers and risks of excessive overtime. However, we know that in many industries workers still rely on overtime earnings. Therefore, if a mechanism to improve wages isn’t established simultaneously, workers’ wages will be adversely impacted. In this instance, perceived ‘improved’ purchasing practices have a negative impact on workers.Everyone should earn a living wage in normal working hours, yet in many global supply chains wages fall well below these levels. Workers rely on earning from overtime to support themselves and their families. In all contexts, it is vital that supply chain partners agree on credible mechanisms to improve working conditions in response to improved purchasing practices. This is even more crucial when living wages are not paid, and where basic enabling rights – such as freedom of association (FoA) – are denied. While the original CFRPP acknowledges this, we have made it more explicit in the introduction to the CFRPPMI to ensure clarity and emphasis.
- Promoting RPP in business-to-business (B2B) partnerships
A new principle added to the CFRPP MI focuses on promoting responsible practices in B2B partnerships. Many manufacturing companies act as both buyers and suppliers, often facing pressure from larger clients—such as state agencies or big brands—to lower prices or meet unrealistic timelines. This pressure can conflict with their desire to improve working conditions. The CFRPP MI stresses the importance of open communication and collaboration in B2B partnerships, encouraging purchasing companies to discuss these challenges with clients and work together towards solutions that ensure fair wages and sustainable practices. - Addressing power imbalances in supply chains
Responsible purchasing practices must address the power imbalances within supply chains. Larger purchasing companies often hold significant influence over smaller suppliers, making it difficult for suppliers to improve conditions. Conversely, smaller purchasing companies may feel powerless when dealing with larger suppliers. However, the CFRPP MI encourages companies to focus on areas they can control and leverage their influence to drive improvements, even in power-imbalanced situations. The role of payment and contract terms
An important update to the CFRPP MI is the inclusion of a principle focused on payment and contract terms. Previously addressed in Principle 4, it is now expanded to include contract negotiations and mutual responsibilities. This change responds to the increasing importance of understanding contract terms in fostering responsible purchasing practices.The updated principle, informed by the Responsible Contract Project, helps companies ensure contracts reflect responsible and sustainable practices. This includes clearly defining mutual responsibilities and ensuring fairness, especially in payment terms. Ethical contract negotiation is crucial for promoting better working conditions and fair wages, making it an essential element of any responsible purchasing strategy.
- Living wages
In designing the CFRPP for the food industry, ETI gave living wages a dedicated section, in recognition of the progress needed in this area. While the original CFRPP acknowledged living wages, the focus on them was less explicit. Given the critical need for workers to earn a wage that "enables them to maintain a decent standard of living", the CFRPP MI includes a dedicated section on living wages, highlighting their role in improving workers' livelihoods and supporting sustainable business practices.
Connecting the CFRPP MI with emerging legislation
As businesses face increasing pressure to uphold human rights and environmental standards, the Corporate Sustainability Due Diligence Directive is shaping the way companies operate. This legislation requires companies to conduct thorough due diligence across their operations, subsidiaries, and supply chains, identifying and addressing risks related to human rights violations and environmental harm.
The CSDDD underscores the responsibility of businesses to review their own operations as part of their due diligence, explicitly stating that purchasing practices and strategies should not contribute to adverse impacts. This is where the Common Framework for Responsible Purchasing Practices in Manufacturing Industries becomes invaluable.
ETI developed a resource that shows how the CFRPP MI corresponds with the CSDDD purchasing practices related requirements, mapping the CFRPP principles to the CSDDD’s articles and recitals to ensure companies can align their purchasing practices with the necessary human rights and sustainability standards. By using the CFRPP MI, companies can align their purchasing strategies with the CSDDD's requirements, helping them stay compliant while also fostering responsible business practices that positively impact both their operations and supply chains.
Moving forward: Advancing responsible purchasing practices
As part of this initiative, ETI has developed a range of resources now available for use, including a report on our findings, the CFRPP MI in four languages—Bengali, English, Hindi, and Mandarin—case studies on RPP from participating organisations, and an online resource outlining how the CFRPP MI aligns with the CSDDD’s purchasing practices requirements.
[1] The Common Framework for Responsible Purchasing Practices (CFRPP) was developed in 2022 by The Ethical Trading Initiative, Ethical Trade Norway, the German Partnership for Sustainable Textiles (PST) and Fair Wear Foundation.